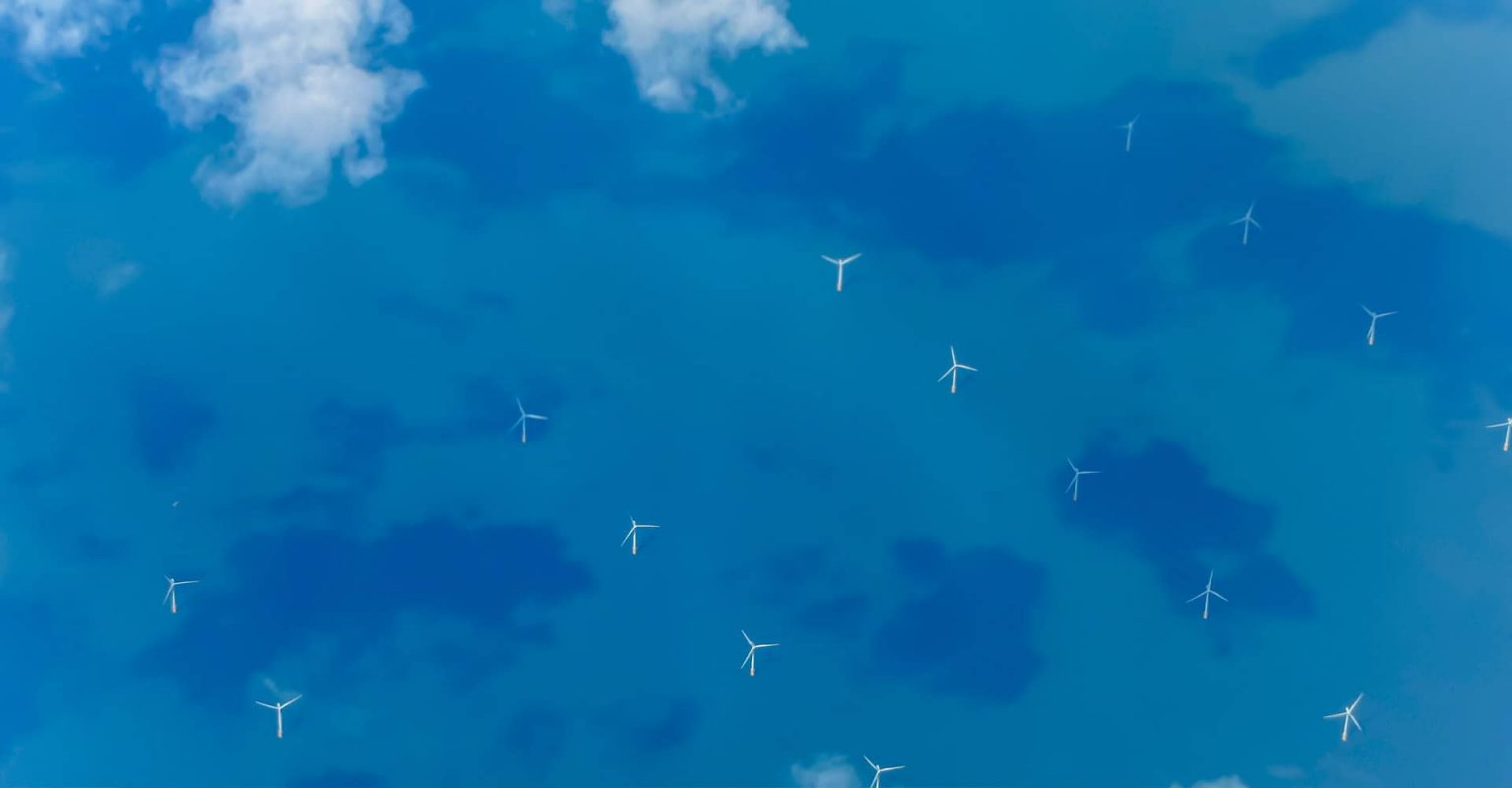
A Problem Shared – Why digital twin technology is the future of offshore wind asset maintenance.
With the 5.5GW of new offshore wind capacity cleared under the UK’s recent Contract for Difference auction, record-low prices of under £40/megawatt-hour, and a future industry target of 30GW by 2030, the UK continues to lead in terms of installing and operating more offshore wind than any other country.
Yet, as the industry matures, it means more turbines emerging from their warranty periods. With each successive wave of construction featuring bigger wind farms further from shore, the stakes are higher when it comes to managing these assets.
Operators want to maximise productivity. Doing so means reducing unplanned downtime to zero. But the traditional approaches to maintenance, based on planned, or scheduled, inspections require transferring personnel to offshore wind farms – high risk environments – many, many miles from land.
While the Offshore Wind Sector Deal is good for the UK’s efforts to decarbonise energy supply, the 30GW by 2030 target can only be achievable while ensuring energy consumers and billpayers are not paying the price of expensive energy.
These factors are creating opportunities for new approaches to asset management in offshore wind, based on data and digitalisation.
Offshore wind O&M costs.
As a proportion of an offshore wind farm expenditure, operations and maintenance (O&M) cost estimates vary. The Offshore Renewable Energy (ORE) Catapult estimates O&M accounts for 25% of the total lifecycle cost of an offshore wind farm.
According to figures quoted by Decom North Sea and member company Bureau Veritas, offshore wind O&M accounts for around 40% of combined, undiscounted lifetime capital expenditure (CapEx) and operational expenditure (OpEx) costs, with unplanned outages resulting in costs of around £10,000 a turbine a day, from loss of generation revenue, maintenance crew salaries and vessel charter.
ORE Catapult’s Digital Innovation Priorities Survey, carried out among offshore wind industry stakeholders, found that O&M presents a key opportunity for data and digitalisation as these technologies can reduce these costs, to further push down the levelised cost of energy (LCoE) of offshore wind.
In the survey respondents said the highest levels of beneficial impact from data and digital technologies, across a wind farm’s entire lifecycle, occurred at the O&M stages, as well as the earlier site assessment and development stages.
Of those companies providing services based on software and digital technologies, digital twin software modelling and machine learning applications were cited as the key trends with potential to transform how offshore wind farms are managed.
Digital twin technology for offshore wind O&M.
The traditional planned/schedule maintenance approach to O&M is based upon doing on site inspections in a high-risk environment out at sea, adhering to standards and best practice norms.
According to Ramboll offshore wind operators face the challenge of how to deal with and process large amounts of data generated by offshore wind farms as they operate. The digital twin of an offshore structure, such as a wind farm’s turbine, bridges this gap between the design and the real condition of the asset once it is installed and begins operations.
Turbines at sea are rich in data.
The data relating to an offshore wind farm’s operation can come from numerous, disparate sources, all stored in different places and in different formats, ranging from real-time operational SCADA and condition monitoring, generated by sensors within various wind turbine components, as well as manually collected inspection data, computer generated drawings and blueprints of structures and plans, operating manuals, and maintenance procedures.
Pooling all the information into a centralised database and feeding relevant real-time data on structural health and performance of the real asset at sea into a three-dimensional version, creates a digital twin of the asset.
By analysing the digital twin, operators can make decisions about precisely what O&M action is needed, such as components that may need upgrading when any other type of intervention is necessary.
Digital twin technology, according to Ramboll:
- Improves understanding of the offshore wind farm
- Lowers the cost of O&M
- Exploits opportunities for lifetime extension beyond the asset’s original design lifetime
The cost of O&M is lowered because operators can enable a risk-based approach to O&M, reducing unplanned repairs and interventions, lowering costs, such as by reducing time vessels are chartered for O&M campaigns and improving health and safety on wind farms by ensuring that wrench-time comprises O&M activity informed by predictive analysis of precisely what needs doing.
Recent Developments.
Certification services provider Bureau Veritas and ORE Catapult are jointly developing an interactive digital twin of the 7MW Levenmouth demonstration wind turbine in in Fife in Scotland.
The collaboration builds on ORE Catapult’s work with several partners to collect and pool together real-time operational and condition monitoring information, as well as other disparate sources and using digital twin software developed by Bureau Veritas’ offshore and marine business.
Ramboll, which first deployed digital twin technology in 2006 on oil and gas structures in the North Sea, has since been refining its technology for the offshore wind industry and recently began testing its technology in the EU-funded ‘Reliable OM decision tools and strategies for high LCoE reduction on offshore wind’ (ROMEO) project.
As part of the five-year project, which started in 2017, the company’s digital twin technology is being used at the Wikinger offshore wind farm off the coast of Germany and the East Anglia One offshore wind farm off the east coast of England.
According to software technology company Akselos, ‘finite element analysis’, the numerical method typically used for the development of digital twin software, has certain limitations when modelling large-scale assets for inclusion of condition details, such as cracks, damage, or corrosion.
Akselos has developed proprietary digital twin software, using its Reduced Basis FEA technology, to create a 3D model of large-scale infrastructure.
Over the past two years Akselos has been working with Shell, to reduce OpEx and extend the life of ageing offshore oil and gas assets. The energy company uses the software to influence operational decisions, optimise operations and safely extend the life of ageing assets.
In mid-2019 the American Bureau of Shipping (ABS) partnered with Akselos to commercialise its digital twin software as part of advanced digital services, offered by ABS, targeting marine and offshore assets.
More recently Akselos and ABS are have formed a consortium led by floating offshore wind company Principle Power, which has received funding from the US Department of Energy to develop, validate, and operate the company’s digital twin software on the WindFloat Atlantic (WFA) project, off the coast of Portugal. In the project the sensor-enabled digital twin will respond in real time to reflect the asset’s current condition, enabling active control of asset integrity and operations.
Challenges and opportunities for digital twin technology in offshore wind O&M.
Since offshore wind farms and turbines lend themselves to harvesting vast amounts of data from diverse sources, predictive analytics and digital twin modelling could prove disruptive in the industry.
However, at this stage one of the biggest barriers to adopting this technology for O&M as well as other activities remains operators themselves. ORE Catapult’s survey found 94% of participants said there is a gap between the way in which the offshore wind industry currently operates, and how it should be operating in order to extract the full value from data and digital technologies.
According to the Navigant Research’s Advancing O&M Insights for Wind Plants with Digital Twins report, digital copies of operating turbines ‘empowers asset owners and wind turbine manufacturers operating wind turbines to predict and plan for faults and optimise performance of their assets.’
However, ORE Catapult’s Digital Innovation Priorities survey found that just under 100% of respondents said there is a gap between the way in which the offshore wind industry currently operates, and how it should be operating in order to extract the full value from data and digital technologies.
Turbine data accessibility and an unwillingness for organisations to share data with each other were cited as other bottlenecks the industry is currently contending with.
To leverage digital twin technology, Navigant’s report recommends wind turbine manufacturers see themselves as ‘both vendors and customers of the technology’, while independent software-as-a-service vendors ‘mine the market and leverage third-party independence over wind turbine suppliers’. It also advises asset owners implementing digital twins to test and verify the technology.
Work by ORE Catapult and Bureau Veritas, the ROMEO project and Akselos’ collaborations are helping to beat the path for greater uptake of digital twin technology in offshore wind O&M.
Key benefits include reducing offshore wind costs, extending asset lifetime, enhancing health and safety of technicians maintaining these assets, and improving understanding of wind farms.
For more information, contact:
Share this insight